Explore the versatility of plastic extrusion in design
Explore the versatility of plastic extrusion in design
Blog Article
Exploring the Numerous Strategies and Technologies Behind Plastic Extrusion
The realm of plastic extrusion is a blend of technology, innovation, and accuracy, critical to various markets worldwide - plastic extrusion. Advanced equipment, electronic controls, and a range of materials converge in this intricate procedure, creating top notch, long lasting products. As the market progresses, a shift in the direction of lasting materials and smart machinery is obvious. The complying with discussion will lose light on these innovations and techniques, while additionally hinting at the exciting future potential customers of this critical production process.
Recognizing the Basics of Plastic Extrusion
The procedure of plastic extrusion, typically hailed as a keystone in the realm of manufacturing, creates the bedrock of this discussion. In essence, plastic extrusion is a high-volume manufacturing process in which raw plastic product is thawed and formed into a continuous account. It's a method widely utilized for producing things with a continuous cross-sectional account, such as pipes, window frameworks, and weather condition removing. The process starts with feeding plastic products, commonly in the kind of pellets, right into a heated barrel. There, it is warmed and blended until it comes to be molten. The molten plastic is then required with a die, forming it into the wanted form as it solidifies and cools.
The Role of Various Products in Plastic Extrusion
While plastic extrusion is a typically utilized method in manufacturing, the materials utilized in this procedure significantly influence its final output. Various sorts of plastics, such as pvc, abdominal muscle, and polyethylene, each provide distinct homes throughout product. As an example, polyethylene, recognized for its longevity and adaptability, is often made use of in product packaging, while PVC, renowned for its stamina and resistance to environmental variables, is utilized in building. ABS, on the other hand, incorporates the ideal attributes of both, causing high-impact resistance and toughness. The choice of material not just affects the item's physical buildings however additionally impacts the extrusion speed and temperature level. For that reason, manufacturers need to carefully think about the buildings of the product to enhance the extrusion procedure.
Techniques Utilized in the Plastic Extrusion Process
The plastic extrusion process includes different strategies that are essential to its operation and efficiency (plastic extrusion). The conversation will begin with a simplified explanation of the fundamentals of plastic extrusion. This will be complied with by a break down of the process in information and an exploration of methods to boost the performance of the extrusion strategy

Recognizing Plastic Extrusion Basics
In the realm of manufacturing, plastic extrusion stands as a basic process, necessary in the production of a wide range of everyday things. At its core, plastic extrusion involves changing raw plastic product right into a constant profiled shape. This is achieved by melting the plastic, commonly in the type of pellets or granules, and forcing it via a shaped die. The resulting item is a long plastic item, such as a pipeline, panel, or wire covering, that maintains the shape of the die. This economical approach is extremely versatile, able to develop complex forms and fit a wide selection of plastic materials. Basic understanding of these basics allows for more exploration of the more elaborate aspects of plastic extrusion.
Detailed Extrusion Process Breakdown
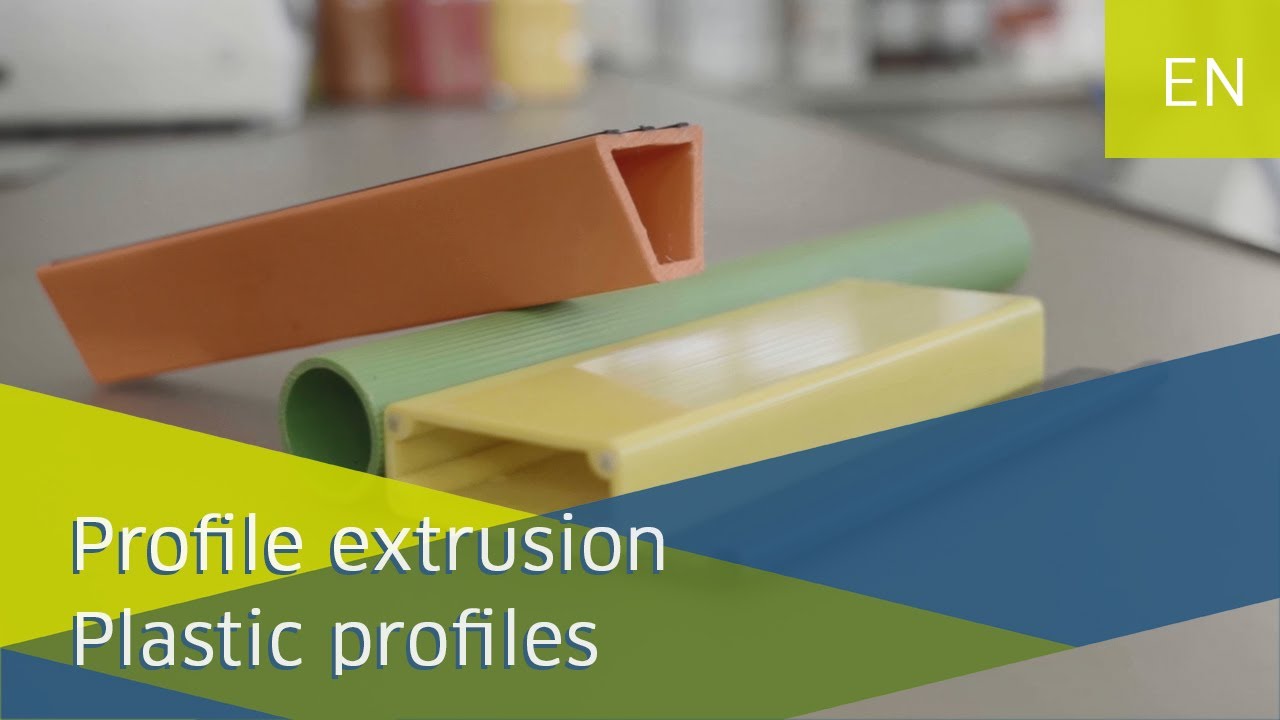
Improving Extrusion Method Effectiveness
Performance gains in the plastic extrusion process can significantly Homepage affect both the top quality of the final product and the overall efficiency of the procedure. Continual optimization of the extrusion technique is crucial to keeping an affordable side. Routine upkeep of extrusion equipment can additionally minimize downtimes, hence increasing efficiency.
Just How Innovation Is Changing the Face of Plastic Extrusion
The development of brand-new technology has significantly changed the landscape of plastic extrusion. It has caused the development of advanced extrusion equipment, which has boosted the performance and high quality of the plastic extrusion procedure. Innovations in the extrusion process have actually additionally been driven by technological improvements, providing improved capabilities and convenience.
Advanced Extrusion Equipment
Changing the realm of plastic extrusion, advanced equipment imbued with advanced innovation is ushering in a new era of effectiveness and precision. These makers, equipped with innovative features like automatic temperature level control systems, ensure optimum problems for plastic handling, therefore reducing waste and enhancing item top quality. High-speed extruders, as an example, enhance outcome prices, while twin-screw extruders provide remarkable mixing capabilities, vital for producing complicated plastic blends. In addition, computerized control systems offer unprecedented accuracy in procedures, lowering human error. These machines are made for longevity, reducing downtime and maintenance expenses. While these advancements are currently amazing, the continuous development of innovation guarantees even better jumps onward in the field of plastic extrusion machinery.
Innovations in Extrusion Processes
Harnessing the power of modern-day technology, plastic extrusion discover here procedures are going through a transformative metamorphosis. With the arrival of 3D printing, the plastic extrusion landscape is additionally broadening into brand-new realms of opportunity. These technological innovations are not only boosting the top quality of extruded plastic products yet additionally driving the market in the direction of a much more sustainable, effective, and cutting-edge future.
Real-World Applications of Plastic Extrusion
Plastic extrusion, a functional and reliable process, finds usage in numerous real-world applications. The vehicle sector additionally uses this technology to produce parts like trim and plastic sheeting. The stamina and versatility of plastic extrusion, combined with its cost-effectiveness, make it a vital process across different industries, underscoring its widespread practical applications.
The Future of Plastic Extrusion: Forecasts and Fads
As we look to the horizon, it comes to be clear that plastic extrusion is poised for considerable innovations and change. Environment-friendly alternatives to standard plastic, such as bioplastics, are also expected to obtain grip. These patterns show a dynamic, progressing future for plastic extrusion, driven by technological development and a dedication to sustainability.

Verdict
In conclusion, plastic extrusion is a complex process that utilizes advanced modern technology and differed products to develop varied items. As plastic manufacturing continues to develop, it remains an important part of several sectors worldwide.
In essence, plastic extrusion is a high-volume manufacturing procedure in which raw plastic product is thawed and developed into a continual This Site profile.While plastic extrusion is a frequently utilized technique in production, the products used in this process substantially affect its final output. At its core, plastic extrusion entails changing raw plastic material right into a constant profiled shape. It has led to the advancement of advanced extrusion equipment, which has enhanced the performance and high quality of the plastic extrusion process.In verdict, plastic extrusion is a complex procedure that makes use of sophisticated technology and differed materials to create varied items.
Report this page